Quality Assurance vs Quality Control
Understanding Their Unique Roles in Quality Management
Quality Assurance (QA) is a proactive approach that establishes procedures, guidelines, and best practices to ensure quality products reach the end user. In contrast, Quality Control (QC) is a reactive approach that identifies and corrects issues arising in the development phase, ensuring that the final product meets pre-defined standards and compliance.
Menu
Quality Assurance vs Quality Control : An Introduction
‘Quality assurance vs. Quality control,’ while both ensure superior quality products or services, their roles, objectives, and methodologies significantly differ from each other. The blurred line between QA and QC often leads to missteps in implementing the overall quality management strategy. Indeed, many organizations that fail to distinguish between QA and QC end up facing repeated defects, excessive testing, compromised product quality, non-compliance with industry standards, and, eventually, customer dissatisfaction.
When comparing quality assurance and quality control, what should we really be focusing on? Are these two approaches entirely separate, or do they have something in common? And what if we integrate them both? Let’s start with the basics and dive into these important questions together.
What is Quality Control (QC)?
Quality control is a structured framework to ensure that the product or service meets the pre-defined standards and expectations. Being a critical aspect of a quality management strategy, it involves a reactive, product-oriented approach for inspection, testing, and monitoring to timely identify and correct the defects or non-conformities.
Core Elements of Quality Control:
- Clear Quality Standards: These act as pre-defined benchmarks for the quality of the final product.
- Streamlined Processes: It ensures the product meets internal and external quality standards.
- Regular Inspection and Testing: Identifies quality events like incidents or non-conformities.
- Corrective and Preventive Actions: It addresses and prevents issues from recurrence.
What is Quality Assurance (QA)?
Quality assurance refers to a broader concept that offers a proactive, process-oriented approach to ensure the product or services meet the set quality standards and customer’s expectations. Quality assurance, as a process, tries to prevent quality events by optimizing processes and implementing effective quality management practices.
- Regulatory Standards: All processes follow a predefined benchmark or industry standards.
- Reliable Processes: All processes are consistent and optimized for better output.
- Early Risk Prevention: Detect and address quality events in the early development phase.Â
- Continuous Improvement: Conduct thorough audits and feedback for enhanced quality.
Differences Between Quality Assurance and Quality Control
Quality assurance and quality control, often used interchangeably, are two different approaches to maintaining quality. While quality assurance focuses on implementing and enhancing quality processes, quality control, on the other hand, identifies defects and non-conformities in the final product.
To bring it to life, picture QA as a production supervisor who sets standards, outlines protocols, and trains employees, ensuring a standard process is followed to avoid deviations and issues. Now, the QC is the final product inspector who conducts thorough testing on each product to ensure it is free from defects and meets the customer’s expectations. Let’s assess both QA and QC based on different criteria.
Aspect | Quality Assurance (QA) | Quality Control (QC) |
---|---|---|
Approach | It is a proactive approach that involves process improvement to prevent a quality event from occurring. | It is a reactive approach that aims to detect and correct errors once they occur. |
Scope | Comparatively, it is a broader concept that involves entire quality processes that impact the quality of the product throughout production. | As it is focused on identifying defects, it involves specific stages of the production phase and prioritizes the end result. |
Activities | A well-planned quality assurance strategy includes developing and documenting SOPs, standards, and protocols; process design and improvement; employee training; risk assessment and mitigation; conducting internal audits; supplier evaluation and management; and more. | The quality control process involves detecting and logging issues, conducting statistical analysis, performing root cause analysis, implementing corrective and preventive measures, fixing defective products, etc. |
Outcome | Quality assurance strategy, when implemented correctly, empowers organizations to foresee potential quality issues before they occur, ensure consistency, reduce manual errors, and carefully review and enhance the existing processes. | On the other hand, a well-implemented quality control strategy reduces the impact of a quality event, effectively prioritizes quality events, minimizes defects, and examines the actual cause of the incident. |
Quality Assurance vs Quality Control: Key Similarities
While quality assurance and quality control differ in their approach, scope, and outcome, they share a few similarities that can strengthen overall quality management.
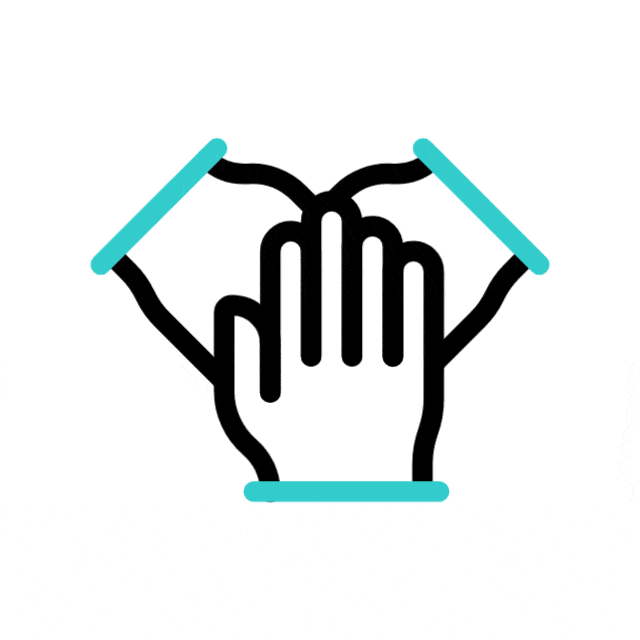
Involvement of Team Collaboration
Implementing a successful quality process in isolation is impossible—it needs seamless collaboration within the organization. However, both QA and QC need a collaborative environment to effectively plan and implement processes (QA) and identify and resolve issues (QC), ensuring overall quality and compliance.
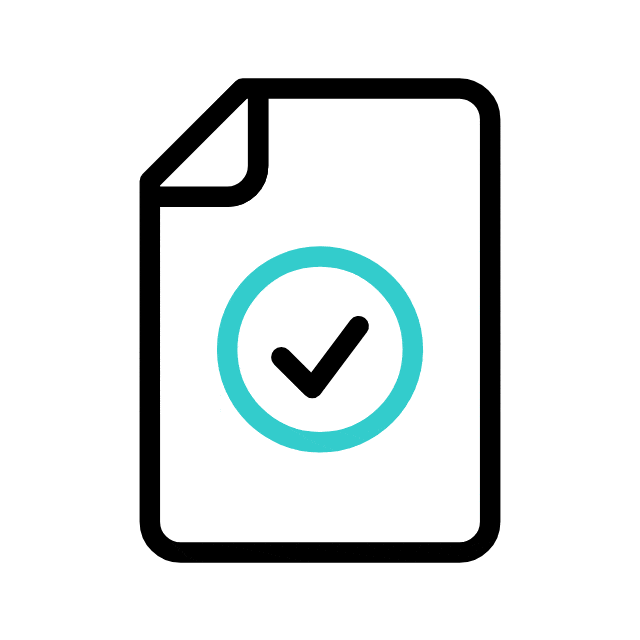
Standardization and Documentation
Both QA and QC rely on effective documentation and standardization to achieve their desired results. Whether they are SOPs, process documentation, and guidelines in QA or predefined inspection protocols and inspection reports in QC, both ensure that the quality-related records are well-documented, consistent, and accessible.
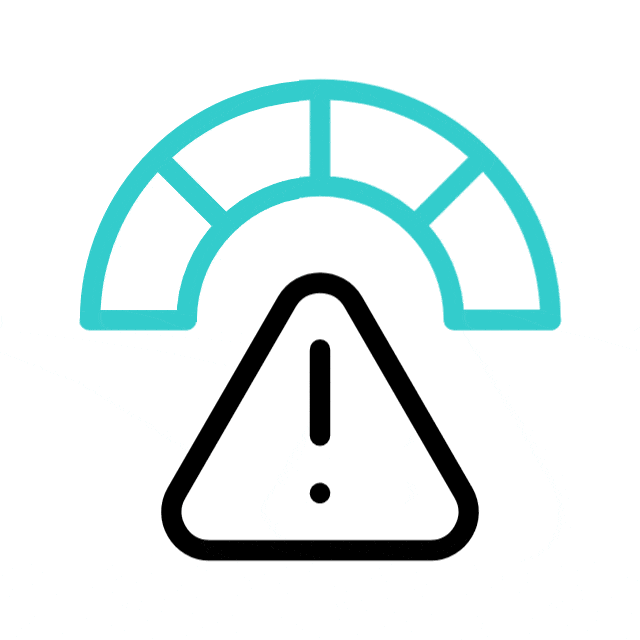
Focus on Risk Management
Risk management is an essential aspect of both quality assurance and quality control. While QA proactively develops processes to detect risks at the early production planning and implementation stages, QC helps identify and resolve risks post-production, ensuring the right product reaches the customer.
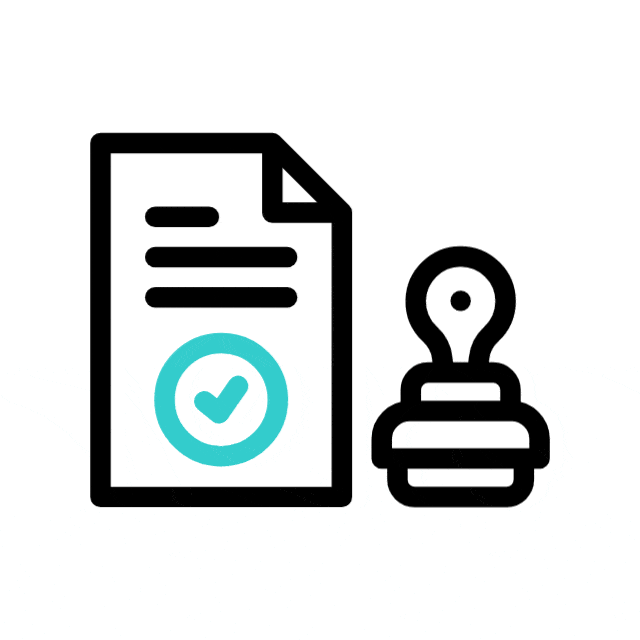
Standard Compliance
Many compliance standards, including ISO 9001, Good Manufacturing Practice (GMP), Good Laboratory Practices (GLP), and more, mandate a systematic procedure for QA and QC. While QA establishes processes that adhere to the compliance standards, QC checks whether the finished product meets the required compliance standards.
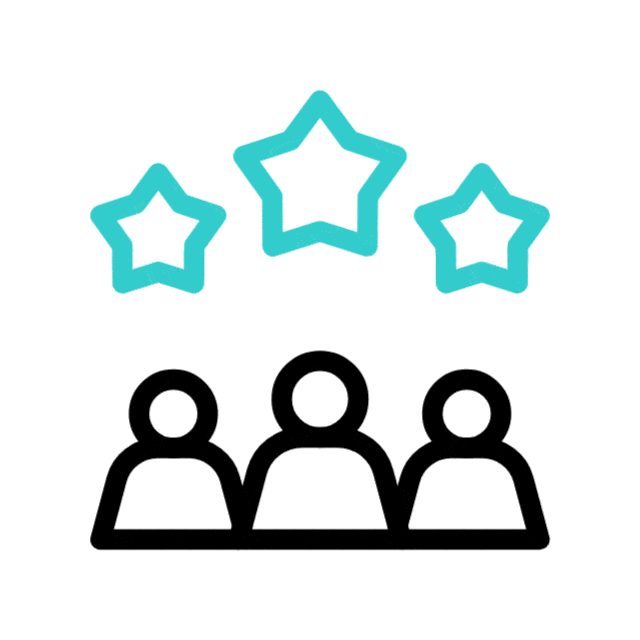
Customer Satisfaction
Both QA and QC focus on delivering quality products or services that meet the end user’s expectations. It eventually optimizes quality processes within the organization, ensuring customer satisfaction and trust.

Got questions about QMS? Our experts are here to help
Quality Management: Integrating Quality Assurance and Quality Control
Integrating quality assurance and quality control is like forging a powerful, strength-based business partnership, where each partner utilizes their individual strengths, resources, and expertise to cultivate mutual success.
When QA and QC work in harmony, they create an exceptional environment for effective quality management. QA is a strategic planner that creates guidelines, establishes protocols, and outlines processes that adhere to regulatory standards. QC, on the other hand, inspects, tests, and verifies the end products for compliance with customer demand.
Key QMS Features for Quality Assurance and Quality Control
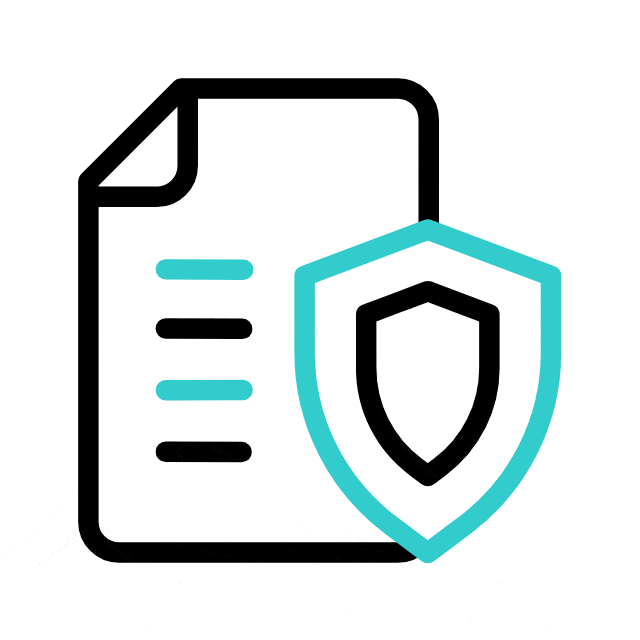
Document Control
Includes features such as versioning, audit trails, access control, and more to ensure all quality-related documents, manuals, and guidelines are organized, secure, and accessible for both QA and QC teams.
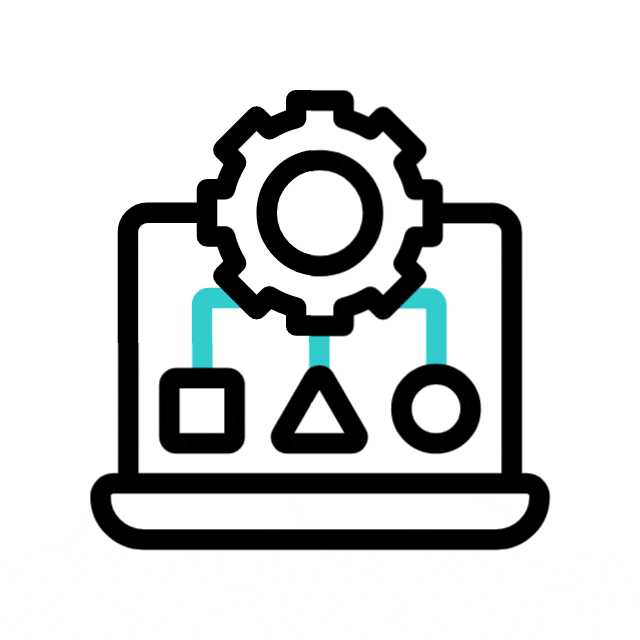
Standard Operating Procedures
It helps establish, store, circulate, and standardize clear SOPs for QA and QC teams to ensure access to the latest resources while maintaining consistency within the organization.
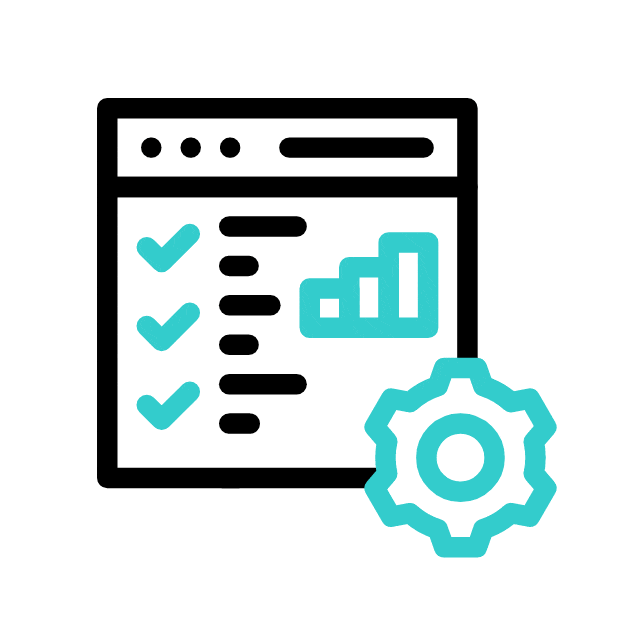
Non-Conformance and CAPA Management
It serves as a centralized platform for both QA and QC teams to identify and log incidents and implement effective corrective and preventive measures for immediate and long-term improvement.
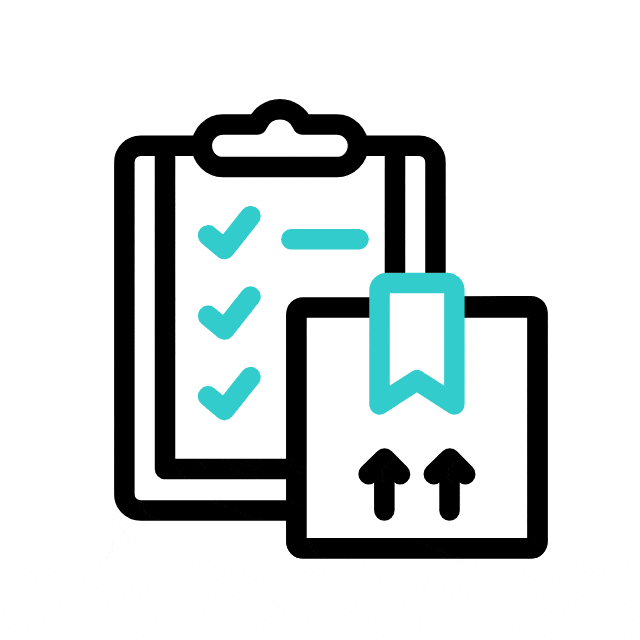
Audit Management
A well-structured audit helps users ensure that the quality process adheres to compliance standards while serving as a robust tool to identify product defects at various stages of the production phase.
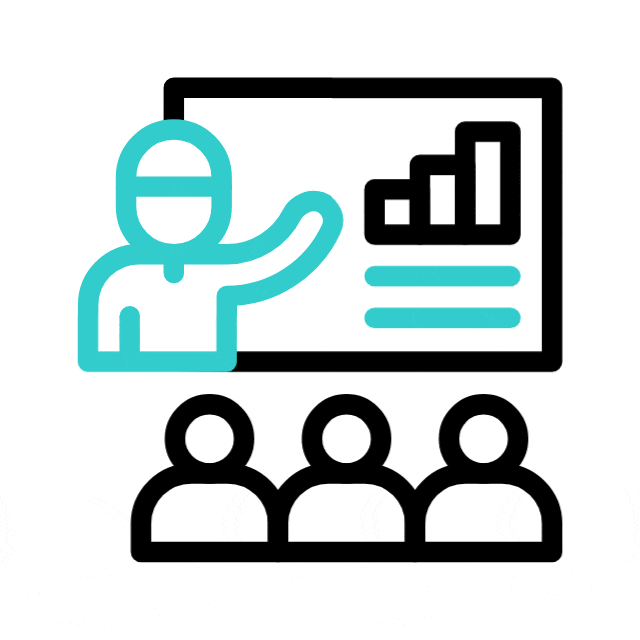
Training Management
A QMS with a dedicated training management module empowers users to train both QA and QC teams, assess and enhance staff skills, and offer access to the latest training resources—all in one place.
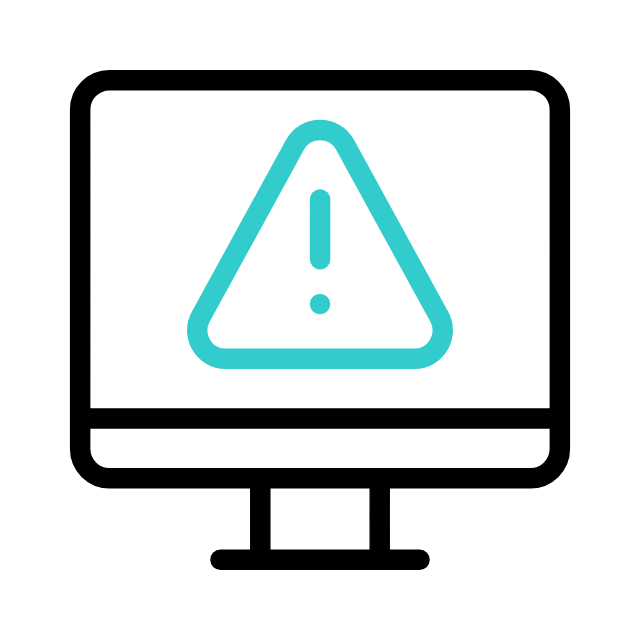
Risk Management
Effective risk management helps teams to proactively detect potential issues and develop as well as implement risk mitigation plans, preventing major quality failure.
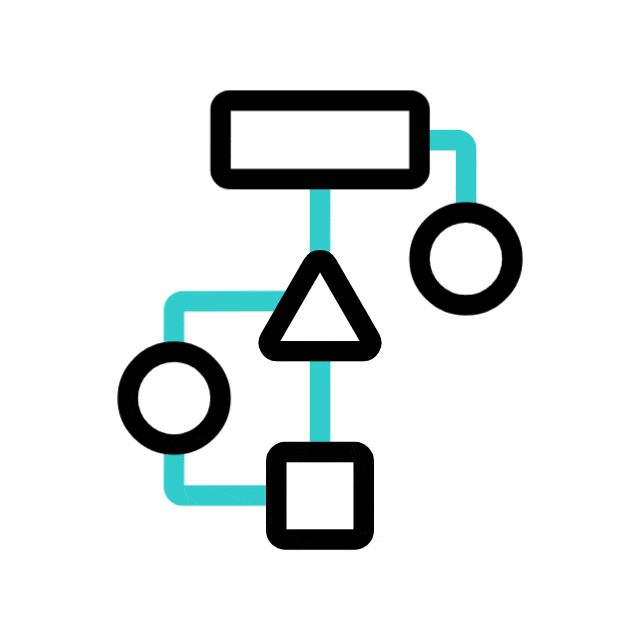
Automated Workflows
Integrating automated workflows helps optimize and fasten the quality management process. Both QA and QC teams can automate document approval, set email reminders, and track and record changes, ensuring transparency and accountability.
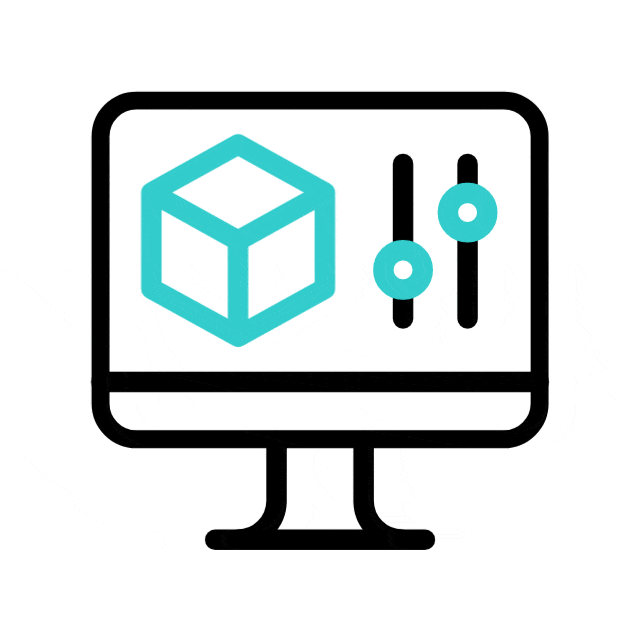
Configurability
A configurable QMS allows both QA and QC teams to adjust processes in response to internal audits and performances. While QA can modify approval and risk assessment workflows, QC can tailor inspection schedules, customize form templates, and more for better productivity.
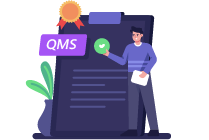
Master the QMS selection process with our comprehensive Buyer’s Guide.
BizPortals QMS: Delivering a Holistic Approach to Achieve Your Quality Objectives
The discussion on Quality Assurance vs. Quality Control highlights both differences and similarities between the two concepts. However, it is clear that integrating both with your quality management strategy can help achieve the highest quality products and services.
BizPortals QMS, a SharePoint-based quality management system, seamlessly integrates both QA and QC functionalities. With a powerful, centralized ecosystem to plan, implement, and audit your quality management strategy, it offers numerous features that foster cross-functional collaboration, decision-making, and continuous improvement.
Along with the dedicated modules to manage SOPs, incidents, deviations, risks, CAPA, audits, trainings, and more, BizPortals QMS offers features like versioning, cross-module integration, automated workflows, e-signatures, role-based access, etc., to enhance both productivity and compliance with regulatory standards.
Whether you are looking for prevention or detection, BizPortals QMS helps you maintain consistent quality excellence. Schedule a free live DEMO, consult with our experts, and explore its robust features firsthand.
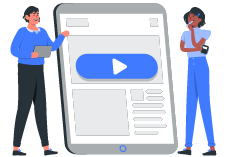